夏杰生
2021年,中國汽車銷量2652.8余萬輛,已連續多年穩居世界第一。乘用車進入家庭,中國市場成為各整車企業競技的舞臺,同時中國自主品牌汽車異軍突起,日益成為中國汽車工業的主力軍。
01 高強鋼用量增長汽車輕量化保障
汽車多用高強鋼,萬千零件來組裝。據中信金屬公司主管汽車新材料研發的路洪洲博士介紹:汽車通常是由車身、發動機、底盤和電氣設備4大部分組成,其中車身、發動機、底盤強烈依賴于金屬材料和制造工藝的發展。
回顧中國汽車輕量化發展的歷程,前些年,自主品牌的乘用車車身高強度鋼平均用量不足30%,很多自主品牌的乘用車車身高強度鋼用量甚至少于10%,與國際先進水平存在巨大差距。經過汽車上下游行業單位和中信金屬等的協同合作及多年耕耘,2021年中國自主品牌轎車先進高強度鋼應用已達到60%以上,達到國際先進水平。
目前 ,汽車輕量化已上升到國家戰略層面,不僅《中國制造2025》將輕量化列為節能與新能源汽車發展的核心技術,在工信部、國家發改委、科技部等國家部委相繼發布的專項方案中,也多次對輕量化技術的發展提出了具體要求。
“綠水青山就是金山銀山”,在汽車節能的諸多途徑中,輕量化歷來被認為是最為有效的、共性的實現方式之一。行業研究表明,汽車每減重10%,燃油節約6%-8%。乘用車整備質量減少100kg,百公里油耗可降低0.3L-0.6L。高強度鋼的開發和應用是汽車輕量化的重要途徑。
2010年中國鈮微合金化汽車鋼板的產量不足500萬噸,到2021年,鈮微合金化汽車鋼板的產量近2000萬噸以上,約占整體汽車用鋼的40%,極大地支撐了中國汽車工業的發展以及汽車工業節能減排的進程。
02 點鈮成金提升鋼材性能品質 見微知著確保汽車綠色安全
中信金屬與國內產學研用的產業鏈各方圍繞汽車鋼開發和應用的國內外差距,設立了50余項產業鏈技術合作項目,先后與上下游開發了輕量化車架及材料、輕量化車輪及材料、輕量化懸架及材料、輕量化車身構件及材料、輕量化半掛車及上裝和材料、高性能齒輪及材料等一系列高性能輕量化汽車總成、零件的成套解決方案。
從乘用車用高強鋼的研發和使用情況來看,路洪洲認為,近年來國內熱沖壓成形鋼零件用量猛增,鈮微合金化材質性能提升。在過去的十幾年間,中國乘用車開始批量應用熱沖壓成形鋼零件,其年產能超過10000萬件。但熱成形零部件存在韌性不足和氫脆延遲斷裂問題。為解決新的熱沖壓成形汽車零件的彎曲性能不足,進而導致高速碰撞時構件提前碰撞斷裂傷害駕乘人員的問題,奔馳和寶馬要求熱成形鋼的彎曲角度必須超過60度和65度(在熱沖壓成形零件上取樣進行彎曲測試)才能夠被采購和使用。國內上下游合作,創新性地提出了采用鈮微合金化開發高彎曲性能、抗氫致延遲斷裂的熱沖壓成形鋼;國內鋼廠與汽車企業合作,通過復合微合金改善熱成形鋼的淬透性,擴大工藝窗口,提高冷彎性能和抗氫脆延遲斷裂性能,所開發鋼種的極限尖冷彎性能以及抗氫脆性能比常規的熱成形鋼22MnB5提高了10%以上,新材料在多個整車企業和多個車型上應用,保證了汽車的被動安全性能,相關創新成果獲得了汽車工業科技進步獎一等獎。2021年含鈮熱成形鋼年產量近10萬噸。
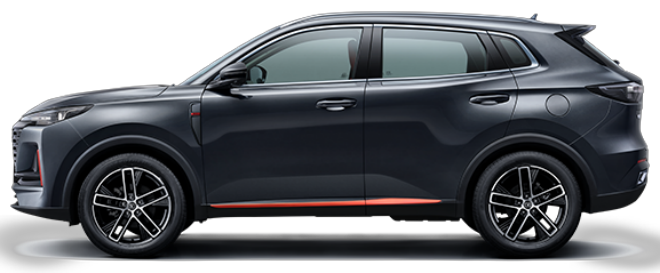
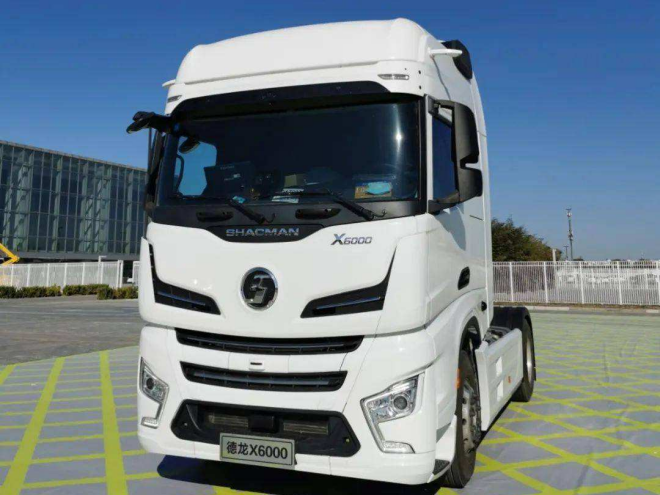
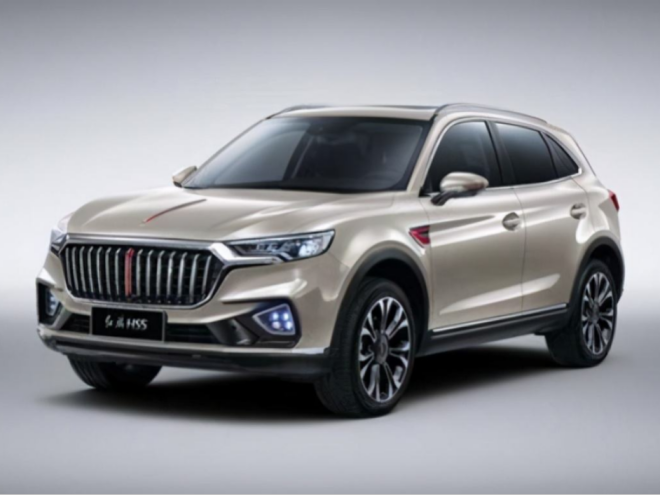
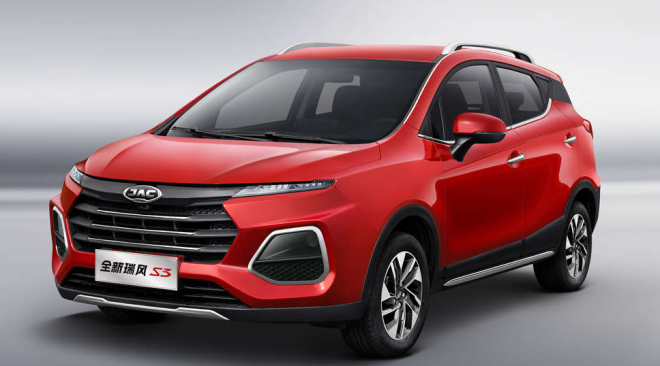
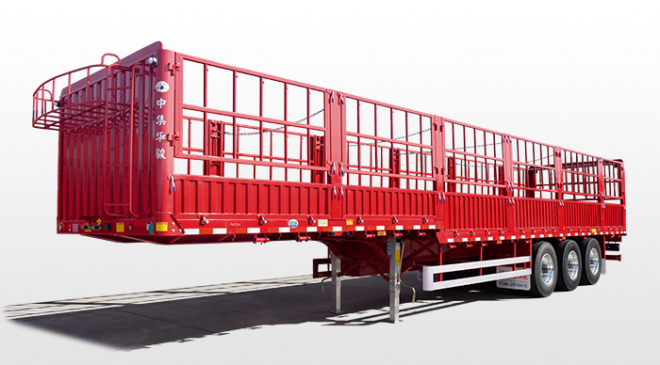
不同車型圖
研究應用問題背后的科學問題,通過氫脆機理提出改善氫脆方案。采用冷鏈原子探針層析技術、氫的同位素氘作為介質,系統研究晶界、位錯、碳氮化鈮的氫陷阱作用機制,在頂刊《科學》主刊發表,提出了高強度鋼汽車鋼氫脆的四個觸發條件,并探討了基于HELP、裂紋鈍化和HEDE的新氫脆機制,一系列宏觀實驗結果與顯微觀察相吻合。在此基礎上,進一步完善了含鈮熱成形鋼及熱沖壓成形零部件的制造工藝。
充分發揮鈮在雙相鋼中重要作用,顯著改善其冷彎及擴孔成形性能。在本世紀初,乘用車車身應用的雙相鋼基本上是以DP590為主,隨著汽車輕量化的快速發展,更高強度級別的雙相鋼如DP780、DP980得到了越來越多的應用。為提高高強雙相鋼的冷彎及擴孔等成形性能,鈮元素發揮了重要的作用。鈮在雙相鋼中的作用是通過細化雙相組織改善材料的成形性。2013年,國內完成了含鈮DP780冷軋鋼板的開發,通過采用含鈮的低碳成分設計,材料的組織得到了顯著改善,冷彎及擴孔等成形性能得到了大幅度提高,為解決零件的剪切邊緣開裂奠定材料保障。
汽車輕量化高強HSLA鋼用量大,穩定性隨強度提高難題迎刃而解。高強低合金鋼主要用于A柱上部加強件、車門檻加長件、前部內側框架、內側B柱、后部發動機支架和內部側框架等,在乘用車白車身中占有很大的比重,是汽車白車身的主要用鋼品種。隨著汽車輕量化發展,汽車白車身采用的冷軋高強低合金鋼強度越來越高,從屈服強度260MPa級別逐步發展到今天的800MPa級別,而高強冷軋HSLA鋼板強度穩定性控制則是一個行業難題,為此,2015年通過與國內大型鋼廠合作,通過軋制及連退工藝優化,成功解決了隨著材料強度的不斷提高,鋼板強度穩定性變差的難題,卷內性能差異<20MPa鋼卷比例由72%提高至98%以上,最大性能波動由94MPa降低至43MPa,卷內性能穩定性效果提升明顯。
用傳統生產線生產含鈮Q&P鋼,為乘用車輕量化提供了新選擇。隨著乘用車輕量化發展的需求,Q&P鋼在國內的專業生產線上得以開發成功并得到實際應用,如何在傳統生產線上生產Q&P鋼,則是一個重要的課題。2018年中信金屬與馬鋼合作開發了1000MPa基于傳統生產線的含鈮高強度、高延性、低成本第三代先進高強度鋼,材料具有和專用產線材料相當的性能,在汽車廠進行了零部件試制,沖壓工藝穩定、零件尺寸精度合格,滿足汽車廠要求。
從開裂的問題導向出發,推動汽車材料卡片構建。碰撞開裂和成形開裂的預防主要基于材料性能、同步分析的精準度和制造工藝的控制,除了采用鈮微合金化以及其他成分優化、工藝優化提升材料性能外,精準的材料斷裂卡片和材料本構至關重要,過去5年間,先后與相關研究測試機構完成了含鈮和不含的熱成形鋼、雙相鋼等材料卡片開發,并完成了零件的剪切邊開裂模擬、零件碰撞模擬,以及零件的成形試制和零件的落錘沖擊測試,構建從材料卡片-成形仿真-零件試制-零件碰撞的閉環,促進了汽車的正向開發。
從性能、成形、成本多維度推動汽車正向選材。基于“車身環狀結構”、“新材料卡片”、“成本模型”等開發了汽車車身正向選材系統(MISS系統),將車身材料選擇與碰撞性能、車身剛度、成形開裂、成本控制相關聯,從基于經驗轉變為基于邏輯判斷,并免費向全行業開放,為汽車正向開發和合理選擇提供了新路徑,確保了“合適的材料用在合適的地方”。
從商用車用高強鋼的研發和使用情況來看,路洪洲介紹,國內企業連續3年連撰兩會提案,商用車超載管制和輕量化引起高層重視,開展協同技術攻關,促節能減排提產品質量性能。在商用車輕量化方面,前些年,商用車上下游行業強調多拉快跑,導致超載嚴重。而且,商用車主要采用510L、330CL、380CL、Q235、Q345等傳統材料,嚴重制約了新材料、新工藝、新設計的應用,造成了自主品牌商用車與國外商用車在品質和質量方面存在著巨大的差距。中信金屬連續三年撰寫全國兩會提案,如2016年提交的《關于改善物流載貨車輛市場需求和結構調整的提案》、2015年《關于鼓勵使用輕量化商用汽車產品以促進節能減排、減緩空氣污染的提案》等。此外,中信金屬還聯合上下游行業開發了輕量化車架、車輪、掛車等降低了能耗和排放、提高了產品性能和質量。經過行業上下游的協同和近十年的技術攻關,大量的新型零部件、新材料得以應用,商用車整體減重約15%左右,降低了能耗和排放、提高了產品性能和質量。
整車自重的減低提高了運輸效率、降低了對道路的損傷,使交通運輸更綠色、更環保。尤其帶動了上游原材料行業和零部件制造行業的技術提升,也為新GB1589國家標準和國家限超政策的實施奠定了基礎。汽車輕量化帶動了汽車節能減排、被動安全等性能的提升,進而提升了產品的競爭力。同時帶動了零部件制造行業、模具行業、熱處理爐行業、成形及連接裝備行業的技術提升,推動了我國機械制造行業的整體技術進步。汽車輕量化有效降低了原材料的使用量,提高了高性能材料的應用,這對我國“供給側結構性改革”有重要的推動作用。經過上下游多年的努力,610L、700L、750L、540CL、590CL等鈮微合金化高強度鋼材料被大批量應用。
產學研用聯合研發車輪鋼,榮獲汽車工業科技進步獎。國內產、學、研、用各單位密切合作,形成了鋼制車輪輕量化成套技術,獲得了2018年度中國汽車工業科技進步獎。設計制造的22.5×9.00鋼制車輪,承載4000Kg,在滿足各性能前提下,單只車輪自重41Kg,已大批量供貨商用車企業應用。設計制造用于國內市場的22.5×9.00鋼制車輪,承載3550Kg,在滿足各性能的前提下,單只車輪自重約37Kg,已大批量供貨北汽福田、中國重汽。設計制造用于國外市場的22.5×8.25鋼制車輪,承載3350Kg,自重約31.6Kg,達到國際先進水平,已經批量出口。外觀造型美觀的高通風孔鋼制車輪的開發為乘用車鋼制車輪提供了一種新的路徑。近兩年開發了礦用自卸車專用輕量化車輪,車輪重量從60kg以上降至50kg以內,完成了第一輪路試,將為礦用自卸車的輕量化和節能減排和成本降低提供新選擇。
車架用鋼強度顯著增長,與國外差距正逐漸縮小。隨著國內商用車輕量化發展需求,車架用鋼強度有了顯著的增長,與國外的差距逐漸縮小,在過去幾年中,車架用鋼的強度逐步由之前的510L轉為700L或更高強度級別鋼板。2012年國內開發出了高強度、高韌性的車架用鋼,促進了商用車用材高強化的發展需求。近年來,相繼開發了高疲勞性能700L和750L,疲勞強度顯著提升,解決了車架疲勞失效、三面沖缺陷、大梁鋼疲勞強度不足等問題,形成了成套解決方案,為商用車輕量化車架應用保駕護航。