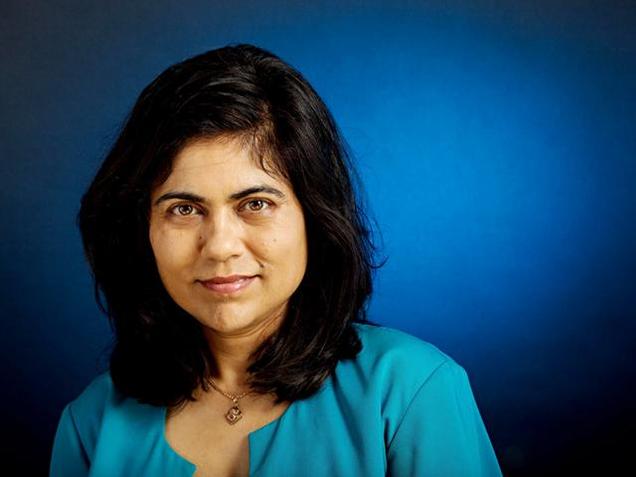
‘Green Steel’ could be the answer to deal with the growing problem of disposal of waste tyres globally.
Mumbai-born scientist Professor Veena Sahajwalla, Director, Centre for Sustainable Materials Research and Technology at University of New South Wales (UNSW) Australia, who has invented Polymer Injection Technology that converts old rubber tyres to metal alloys that make ‘Green Steel’ says this could be the answer to deal with the growing problem of disposal of waste tyres globally.
Excerpts from an interview:
How alarming is the problem of waste tyres globally?
Every year, over one billion tyres are manufactured worldwide, and equal number of tyres are permanently removed from vehicles, becoming waste.
The U.S. is the largest producer of waste tyres, about 290 million a year, although increases in new vehicles sales in China and India are rapidly contributing to waste tyre volumes.
Although modern tyres are fundamentally rubber products, they are a complex mix of natural and synthetic rubbers, and various structural reinforcing elements including metals and chemical additives.
This complexity has led to stockpiling, dumping and diversion to landfill. This has exposed communities to environmental and health risks and has squandered valuable resources locked up in tyre dumps.
Stockpiled tyres are at risk of fire and toxic smoke, the largest tyre fire in the world began in Wales in 1989 at Heyope, where 10 million tyres had been dumped, and took 15 years to extinguish.
Other risks include the stagnant water in tyres that provides breeding grounds for mosquitoes and leaching of toxic substances into soils.
Globally, in 2011, only 7% of waste tyres were recycled on site, 11% were burned for fuel, 5% were exported for processing elsewhere. The remaining 77% were sent to landfills, stockpiled, or illegally dumped; the equivalent of some 765 million tyres a year wasted.
How about India?
India’s waste tyres account for about 6-7% of the global total. With the local tyre industry growing at 12% per annum, waste volumes are rising.
India has been recycling and reusing waste tyres for four decades, although it is estimated that 60% are disposed of through illegal dumping.
Despite this, India is the second largest producer of reclaimed rubber after China. In 2011, India produced 90,000 metric tonnes of reclaimed rubber from waste tyres.
By 2016, some100 000 kms of Indian roads had been laid with asphalt blended with recycled rubber, and over 500 000 tonnes of crumb rubber modified bitumen (CRMB) is used annually in road construction. New regulations introduced in 2016 allow for import of waste tyres for recycling.
What is your technology all about?
We have developed Polymer Injection Technology (PIT), or ‘green steel’ which introduces a simple modification into the conventional manufacturing process for steel. The technology precisely controls the injection of granulated waste tyres in conventional Electric Arc Furnace (EAF) steelmaking, partially replacing non-renewable coke.
Waste tyres, like coke, are good sources of hydrocarbons. This means they can be usefully transformed in EAF steelmaking, as long as the process of injecting them into the furnace is precisely calibrated.
UNSW spent a number of years researching and understanding the high temperature reactions that take place when waste tyres partially replace coke, enabling us to optomize the operating parameters of the furnaces.
Consequently, millions of waste tyres are already being transformed into high quality steel in Australia, and around the world.
Can this technology be applied in India?
Yes, it is ideal for application in India as it is incorporated into conventional EAF steelmaking, so it does not require expensive new industrial infrastructure or any large scale new equipment.
What went into the mind for developing such technology?
My ambition to transform waste into valuable resources goes back to my childhood in India. Growing up in Mumbai, I used to walk past huge mountains of garbage on the way to school which supported communities of rubbish pickers. I imagined what it would take to convert “rubbish” into something more valuable, like a resource for steelmaking.
Rubbish pickers would then have something more valuable to sell and we could improve the environment and reduce costs for steelmakers. That was part of my drive to first study Material Sciences in India, and to then go onto post-graduate and post-doctoral research in Canada and later in Australia, where I have worked at the UNSW in Sydney since the mid-1990s.
To realise this ambition, I knew that we needed to do something really significant; we needed to revolutionise recycling science.
The world’s waste mountains are packed with materials that contain valuable elements like carbon, hydrogen, silicon and metals that we would otherwise source from virgin raw materials.
That was the idea of looking at waste tyres as a potential resource — they are valuable hydrocarbons.
Why is it necessary for India to convert waste tyre into metal?
Steel is one of the most important materials worldwide. As India’s economy grows, so does its demand for steel. ‘Green steel’ offers multiple benefits – as it makes good use of waste tyres, it reduces the cost of EAF steelmaking and reduces the environmental footprint of the industry.
What is normally done with waste tyres?
Most waste tyres end up in landfill. With our ‘green steelmaking’ process we have introduced a real economic and environmental incentive for communities and businesses to value waste tyres as an input into steelmaking, and so steer them away from landfill.
Globally, much positive work has been done to recycle or reuse tyres, but it has not kept pace with the growing volumes.
Some of these uses include burning tyres as fuel in cement kilns, the use of waste tyres in civil engineering works such as retaining walls and highway barriers, the use of granulated waste tyres for numerous applications such as sports and playground surfaces and blended into asphalt for road making or as rubberised asphalt concrete.
Waste tyres can also be burned to generate energy directly.
What are your plans to take this technology ahead?
Our technology has been already integrated into commercial steelmaking operations in Australia, Thailand, South Korea, the UK and Norway, with discussions in process for other locations. We are also exploring other options for EAF steelmaking that eliminate non-renewable fossil fuels entirely.